The world of rally went crazy in the early 2000s. Technical regulations were fairly open, and with no road-car homologation requirement and ever-better computer technology, the stage was set for truly wild machines. Peugeot was the first to really take advantage of the rules with the 206 WRC, but in 2003, corporate stablemate Citroën took things further with suspension technology so clever, McLaren still uses it today.
This story starts further back than the turn of the millennium, though. In the late Eighties, Australian Chris Heyring, then an art professor, came up with an idea for a new type of automotive suspension. His “Kinetic” suspension system seeks to overcome the limitations of traditional anti-roll bars. An anti-roll bar, obviously being a fixed piece of metal connecting opposite sides of the car, is of a fixed stiffness. Some traditional units have a range of adjustments, but once it’s bolted into place, roll stiffness is fixed. You’re stuck with a set “moment (torque) resisting body roll per degree of body roll,” as Race Car Vehicle Dynamics defines roll stiffness, also known as “roll rate.”
Heyring’s solution hydraulically interlinks opposite sides of the car. Essentially, the dampers in a Kinetic-suspension car have separate top and bottom units. The compression units on one side of the car are linked via flow-restriction valves and hydraulic lines to the rebound units of the other side, and vice versa. This essentially creates a hydraulic anti-roll bar. When a wheel compresses, the piston in the damper pushes up on the compression unit, and the fluid in that top unit flows across the car to the rebound unit on the other side, pushing the wheel up towards the body. The stiffness of the roll bar is governed by an accumulator, a metal sphere with fluid and nitrogen separated by a flexible membrane. You can compress a gas, but not a fluid, so when there’s excess fluid in the system, it presses up against the membrane, compressing the nitrogen. (The accumulator operates with the same basic principle as a suspension sphere in a hydropneumatic Citroën, like a DS.) The valves between the damper units and the hydraulic lines regulate damping force.
(Engineering Explained’s, Jason Fenske has a nice visual explanation of the system as used by McLaren, if you’re looking to get a better image of how all this works)
Essentially, the Kinetic suspension decouples vertical wheel motion (compression and rebound) from horizontal motion (roll), while offering a ton of bandwidth when it comes to roll stiffness. Heyring developed the system for off-roaders, where to increase wheel articulation, you really want no anti-roll bar whatsoever. But on the road, going without an anti-roll bar is unpleasant at best, and dangerous at worst. Some Jeep Wranglers have an anti-roll bar disconnect for off-roading, but the bar must be reconnected for driving on the road.
Kinetic, the company Heyring founded to develop the system was acquired in 1999 by American supplier Tenneco. Citroën was up against the dominant Peugeot team, and it thought that the Kinetic suspension system, or at least a version of it, would give its Xsara WRC an edge over the dominant 206 WRC. The Xsara WRC incorporated a sort of split metal anti-roll bar supported by the hydraulic system. It offered Citroën’s rally drivers a car with great flexibility—on rough terrain, each wheel had the bandwidth to handle the many dips, crests, bumps, jumps, rocks, and everything else you see on a rally stage. On faster, smoother roads, you could effectively ramp up roll stiffness for more speed.
This also helped keep the aerodynamic platform more stable. It’s tricky to manage the airflow on a race car that’s constantly moving around, even on a perfectly smooth piece of track—it’s why modern F1 cars, especially in the new ground-effect era, must be so stiff. On the many varied stages of the World Rally Championship, a rally car moves around a hell of a lot more, unlike in a circuit race car, you need wheel travel too. How do you create a nice level aerodynamic platform while also keeping the car soft enough to deal with, say, the dusty stages of the Acropolis Rally? For Citroen, the Kinetic system was the answer, and it was a key part of the machine that turned the team into a WRC powerhouse.
In its racing debut, at Monte Carlo, Citroen took a 1-2-3 finish, proving the might of the Xsara WRC. Petter Solberg won the driver’s championship that year driving a Subaru, but Citroen clinched the constructor’s title, and won both titles in 2004 and 2005, also thanks in large part to a Frenchman named Sébastien Loeb, who took both driver’s titles. “One of the Xsara’s strong points is its capacity to adapt quickly from one terrain to another,” said Loeb of the car in a 2003 Tenneco press release. “Its balance is simply remarkable.”
The WRC, conscious of the rising costs for constructors to remain competitive, banned various high-tech suspension systems including Citroën’s for the 2006 season. Yet by this point, the Kinetic suspension found new life in road cars. The Lexus GX 470 of 2004 was the first production car to license the technology, with Toyota’s adaptation using the hydraulic system in concert with traditional anti-roll bars. Yet, it’s McLaren that licensed it next and ran with this system, creating a novel application for its supercars that offer a freakish blend of ride quality and handling.
“One of the things that you want to be able to do is change your roll stiffness between a kind of road going mode and something representing track stiffness and that with a mechanical setup is extremely difficult to do,” says McLaren Chief Technical Officer Charles Sanderson. McLaren Automotive’s version is called Proactive Chassis Control (PCC), and it debuted with its first modern road car, the 12C in 2011. Sanderson gained much familiarity with the system while working on the P1’s powertrain, and then led vehicle dynamics for the 720S. In 2018 he left McLaren for Rivian, where he adapted this suspension system for the EV startup’s off-road pickup and SUV. He rejoined McLaren just a couple of months ago.
PCC doesn’t use anti-roll bars at all—roll support is generated solely by the hydraulic system. “An anti-roll bar has a linear stiffness, as in, the stiffness doesn’t increase as you turn the roll bar. But when you roll with the kinetic system the shape on a graph is kind of curved, so as you roll, the stiffness increases and you resist roll really nicely,” Sanderson explains. “That means you get quite a compliant ride and then you get a really nice absolute roll angle.” PCC also uses hydraulic pumps which can change roll stiffness depending on drive mode.
The system has a lot of flexibility. In the P1, for example, McLaren added a hydraulic circuit to manage heave, when both sides of the car’s suspension are in compression or rebound at the same time, like in braking. This helped manage the P1’s massive aerodynamic loads. For the 720S, it created PCC II, which integrated new controls to the damping system, based on a predictive algorithm created by a PhD student at Cambridge. The car uses accelerometers to predict what’s about to happen, constantly adjusting the damping rates to suit. The result is a car that rides better than a lot of luxury sedans while providing incredible performance on track. For the new 750S, McLaren debuted PCC III, which features lighter spring-damper units, new accumulators integrated into the damper struts, and other hardware tweaks.
There are other suspension systems out there that can change roll stiffness. Many luxury sedans and SUVs have motors integrated into the anti-roll bars that can change bar stiffness. These are very effective, but relatively slow acting and heavy. Plus, they require a lot of power to run, necessitating a 48-volt system. Even as more powerful electrical architectures become more popular, Sanderson thinks active anti-roll bars will remain undesirable because auto engineers need to fight for efficiency anywhere they can, and a system with a big power draw isn’t ideal. PCC and other similar systems like Toyota’s run off a traditional 12-volt circuit. And all that aside, you still have an anti-roll bar linking the car side to side, reducing the potential for wheel articulation. Then there’s Multimatic’s new fully active spool-valve dampers, which offer as much, if not more flexibility than a Kinetic system, yet also need 48-volt electrics plus a dedicated cooling circuit, which is heavy and expensive. That’s why, for McLaren, PCC is here to stay. Sanderson sees even more unique possibilities as downforce levels on road cars increase in the pursuit of performance.
Too bad WRC teams can’t use it.
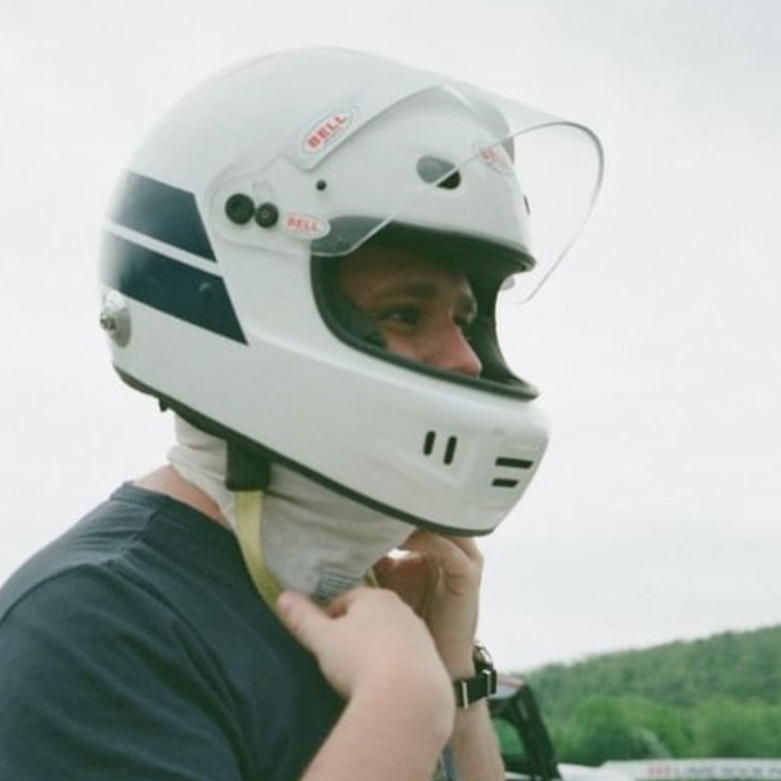
Senior Reporter
A car enthusiast since childhood, Chris Perkins is Road & Track’s engineering nerd and Porsche apologist. He joined the staff in 2016 and no one has figured out a way to fire him since. He street-parks a Porsche Boxster in Brooklyn, New York, much to the horror of everyone who sees the car, not least the author himself. He also insists he’s not a convertible person, despite owning three.