Electric vehicles have gone from parlor-trick city runabouts to the main focus of automaker plans at breakneck speed. In 2011, 10,000 battery-electric vehicles (BEVs) were sold in America, an almost meaninglessly infinitesimal fraction of the 11.5 million cars sold that year. Now, analysts predict that 2023 will be the first year where we see one million BEV sales, and half of consumers say they are actively considering an electric vehicle for their next automotive purchase.
One other meaningful trend is noticeable over this same period, and helps explain how EVs have taken the market so rapidly. In 2011, the average BEV sold in America had a paltry 73 miles of range (which just so happens to be the exact EPA range rating of the 2011 Nissan Leaf, the first truly mainstream BEV). That number has quadrupled in the past twelve years, and the average new BEV sold today has 291 miles of range.
This has helped speed adoption, as consumers demand—by huge margins—that their BEVs have over 300 miles of range, according to studies by both Bloomberg and Cox Automotive. Whether people will use that mileage or not is still up for debate, but it’s clear that without the vast leaps in battery technology that have allowed for 300-mile BEVs, the American market share of electric cars would still be measured in tenths of a percent.
So how have automakers fueled this massive leap in range? The short answer is that while batteries are often marketed simplistically, there are large differences as to how they’re built, managed, and integrated into the cars they power. Here’s how EVs have reached such staggering distances—and how 1000-plus mile battery packs may be in the not-too-distant future.
Cells, Interlinked
Batteries are an older concept than the United States. Indeed, Benjamin Franklin was the first person to coin the term “battery”, in 1760, for a device used to store electrical charge. Batteries are all based on the same fundamental concept: Easily preserved chemical potential energy is stored in an inactive state within the battery. By activating a chemical reaction in the battery and releasing the stored potential chemical energy, electricity is produced.
All batteries contain three components to function: two electrical terminals (known as the cathode and the anode) and a chemical substance separating them, known as the electrolyte. Ions flowing through the electrolyte from the anode to the cathode release electricity; ions flowing in the opposite direction recharge the battery. It is a simple concept, but the implementation can be incredibly complex.
The first rechargeable battery was the lead-acid battery, still in use in cars today to run electrical accesories. Most EVs in the early 20th century and stretching all the way into the late Nineties with the GM EV1 used lead-acid batteries as their source of energy. These are a relatively straightforward implementation of the battery concept, with metallic lead and lead dioxide serving as the cathode and anode, and a sulfur solution of some kind as the electrolyte.
While lead-acid batteries are chemically stable, they have a low energy density for their weight—around 35 watt-hours per kilogram—and they tend to degrade rapidly when run to empty repeatedly. Most early lead-acid batteries used diluted liquid sulphuric acid as an electrolyte, which meant if a battery was tipped over, highly dangerous acid would spill out. These early batteries also needed frequent top-ups with water, which turned EV maintenance into an arduous task. As such, early EVs were heavy, high-maintenance machines, with short ranges and massive battery packs, which kept them from widespread viability for decades.
Big Oil vs. Nickel Hydride
The next major development in electric vehicle technology came from the mind of self-taught American inventor Stanford Ovshinsky in the form of the nickel-metal hydride (NiMH) battery. The NiMH battery improves vastly upon the earlier lead-acid form—it uses nickel hydroxide (the “Ni”) as a cathode, an alloy that absorbs hydrogen as an anode (the “MH”), and a potassium hydroxide as an electrolyte. The potassium-hydroxide electrolyte is less dangerous than the sulphuric acid mixture in lead-acid batteries, and crucially, “NiMH batteries have higher power and energy density and a much longer life cycle compared to lead-acid batteries,” according to John M. German in the Encyclopedia of Energy. This energy density is roughly twice that of lead-acid batteries, at roughly 70 Wh/kg.
According to German, NiMH batteries are popular because they are “completely safe and their power output is not affected by the battery state of charge,” meaning voltage output stays consistent until the battery is fully dead. These are all attractive attributes for automotive applications, and indeed, automakers adopted NiMH batteries not long after Ovshinsky’s invention. Many of the late Nineties and early Aughts “first-wave” EVs—developed as a direct response to California government mandates for alternative-fuel vehicles—used NiMH batteries with some success.
General Motors converted from lead-acid to NiMH batteries midway through the production run of the EV1. This effectively doubled the car’s range over the previous lead-acid powerpacks—albeit with significant issues with battery overheating, as NiMH batteries are highly sensitive to heat.
Toyota also used NiMH batteries in the all-electric RAV4 EV, but after a purchase of the patent by Chevron in 2001 and a subsequent lawsuit against Toyota for copyright infringement, the company was forced to discontinue using these batteries as the sole power source for BEVs. (Toyota still uses NiMH batteries for its hybrid battery packs, as the copyright suit did not cover gas-electric hybrid vehicles.)
Still, the infringement lawsuit has led some to believe that the fossil-fuels industry intentionally attempted to suffocate the BEV in its crib. Although automakers insist the interest just wasn’t there for 100-mile EVs that took 18 seconds to reach 60 mph. (The current market for hyper-quick EVs and the appetite for 300 miles of range seems to support this.) What it took for widespread adoption, then, was yet another battery chemistry that could give buyers the range and power they truly wanted.
The Fifth Track on Nirvana’s Nevermind
The advancement that has finally allowed for 300-mile EVs was the mass-production of large lithium-ion (li-ion) batteries. Li-ion batteries have many different specific forms, but they all share one thing in common—a liquid lithium-salt electrolyte. Li-ion batteries have excellent energy density, up to 270 Wh/kg, or quadruple that of an average NiMH battery. In addition, as Jayam Prabhakar Aditya and Mehdi Ferdowsi explain in a 2008 IEEE paper, li-ion batteries boast “light weight… high specific energy, good high-temperature performance, low maintenance,” as well as a low rate of self-discharge relative to NiMH batteries (meaning they don’t lose charge rapidly when unused).
While li-ion batteries in automotive applications aren’t new—the first use was in the 1998 Nissan Altra EV—they are temperamental and development was arduous. A poorly cared for battery is prone to exploding, and li-ion batteries require large amounts of dangerous materials to build, making mass production challenging. Still, their positive attributes and extremely high energy density were appealing, leading both Tesla and Nissan to pursue li-ion battery packs for mass-market vehicles.
The results were indisputable. Tesla, first to market with a production li-ion battery car in the Roadster, used its early R&D to catch “legacy” automakers off guard; Nissan, with the more mundane Leaf, was the first manufacturer to sell over 300,000 BEVs. The long range possible with li-ion batteries meant they were the first technology to convince the public—and automakers—that BEVs were worth pursuing.
Li-ion batteries in automotive use primarily rely on two different chemical compositions, based on the construction of the cathode. The first and most common type is the nickel-manganese-cobalt (NMC) or nickel-cobalt-aluminum (NCA), which is how the most efficient lithium batteries are constructed. Difficulties with sourcing nickel from Russia in the wake of its invasion of Ukraine, however, have led some automakers to pursue a lithium-iron-phosphate (LFP) cathode construction, which is less energy-dense (at 160 Wh/kg vs. NMC’s peak 270 Wh/kg), but easier to source.
After very early dominance by NMC and NCA batteries, LFP batteries now make up roughly 30% of the new EV market, primarily thanks to Chinese automaker BYD and American automaker Tesla’s growing use. Even with the less-energy-dense LFP batteries, Tesla has still managed to squeeze out nearly 300 miles of range in the standard-range Model 3, meaning the difference between NMC and LFP isn’t as significant as that between, say, NiMH and li-ion, or lead-acid and NiMH.
The differences between LFP and NMC batteries may end up being nothing compared to what’s just on the horizon for BEVs, however.
Ceramic Class Gets Electrified
The next advancement on the horizon for batteries is the solid-state lithium battery. A solid-state battery replaces the (highly reactive and flammable) lithium-salt liquid electrolyte of a traditional li-ion battery with a solid electrolyte (usually, a ceramic of some kind). This virtually eliminates the explosive fire risk of li-ion batteries while simultaneously doubling the energy density and increasing overall longevity. According to Allan Paterson, chief technical officer of battery-tech startup Britishvolt, “Solid-state is the holy grail of battery solutions… [they] could dramatically, and positively, change the world of electric vehicles.” Decades of research on finding a suitable solid electrolyte that doesn’t crack under repeated charging, however, have yielded nothing.
That could change in the coming years, however, as Toyota claims its first solid-state lithium battery—with over 600 miles of range—will be hitting the market as early as 2027. Toyota has recently partnered with Japanese oil firm Idemitsu to begin production of the new batteries, with mass production targeted around the end of this decade. Perhaps, at long last, 600-plus-mile mile EVs will finally cure Americans’ range anxiety. Until then, there’s always the Hummer EV’s 2818 pounds of lithium-ion power to help mask your fears.
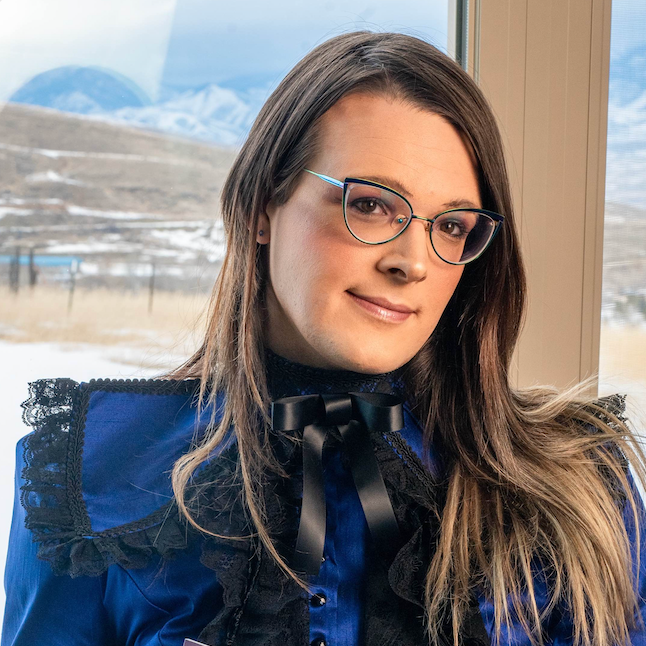
Contributing Editor
Victoria Scott is a freelance writer, photographer, author, and cat mom who lives in Seattle. She is a leading industry expert in catastrophically breaking her vehicles while off-roading. Her proudest moment behind the wheel was completing Mission 34 in Gran Turismo.
Electric vehicles have gone from parlor-trick city runabouts to the main focus of automaker plans at breakneck speed. In 2011, 10,000 battery-electric vehicles (BEVs) were sold in America, an almost meaninglessly infinitesimal fraction of the 11.5 million cars sold that year. Now, analysts predict that 2023 will be the first year where we see one million BEV sales, and half of consumers say they are actively considering an electric vehicle for their next automotive purchase.
One other meaningful trend is noticeable over this same period, and helps explain how EVs have taken the market so rapidly. In 2011, the average BEV sold in America had a paltry 73 miles of range (which just so happens to be the exact EPA range rating of the 2011 Nissan Leaf, the first truly mainstream BEV). That number has quadrupled in the past twelve years, and the average new BEV sold today has 291 miles of range.
This has helped speed adoption, as consumers demand—by huge margins—that their BEVs have over 300 miles of range, according to studies by both Bloomberg and Cox Automotive. Whether people will use that mileage or not is still up for debate, but it’s clear that without the vast leaps in battery technology that have allowed for 300-mile BEVs, the American market share of electric cars would still be measured in tenths of a percent.
So how have automakers fueled this massive leap in range? The short answer is that while batteries are often marketed simplistically, there are large differences as to how they’re built, managed, and integrated into the cars they power. Here’s how EVs have reached such staggering distances—and how 1000-plus mile battery packs may be in the not-too-distant future.
Cells, Interlinked
Batteries are an older concept than the United States. Indeed, Benjamin Franklin was the first person to coin the term “battery”, in 1760, for a device used to store electrical charge. Batteries are all based on the same fundamental concept: Easily preserved chemical potential energy is stored in an inactive state within the battery. By activating a chemical reaction in the battery and releasing the stored potential chemical energy, electricity is produced.
All batteries contain three components to function: two electrical terminals (known as the cathode and the anode) and a chemical substance separating them, known as the electrolyte. Ions flowing through the electrolyte from the anode to the cathode release electricity; ions flowing in the opposite direction recharge the battery. It is a simple concept, but the implementation can be incredibly complex.
The first rechargeable battery was the lead-acid battery, still in use in cars today to run electrical accesories. Most EVs in the early 20th century and stretching all the way into the late Nineties with the GM EV1 used lead-acid batteries as their source of energy. These are a relatively straightforward implementation of the battery concept, with metallic lead and lead dioxide serving as the cathode and anode, and a sulfur solution of some kind as the electrolyte.
While lead-acid batteries are chemically stable, they have a low energy density for their weight—around 35 watt-hours per kilogram—and they tend to degrade rapidly when run to empty repeatedly. Most early lead-acid batteries used diluted liquid sulphuric acid as an electrolyte, which meant if a battery was tipped over, highly dangerous acid would spill out. These early batteries also needed frequent top-ups with water, which turned EV maintenance into an arduous task. As such, early EVs were heavy, high-maintenance machines, with short ranges and massive battery packs, which kept them from widespread viability for decades.
Big Oil vs. Nickel Hydride
The next major development in electric vehicle technology came from the mind of self-taught American inventor Stanford Ovshinsky in the form of the nickel-metal hydride (NiMH) battery. The NiMH battery improves vastly upon the earlier lead-acid form—it uses nickel hydroxide (the “Ni”) as a cathode, an alloy that absorbs hydrogen as an anode (the “MH”), and a potassium hydroxide as an electrolyte. The potassium-hydroxide electrolyte is less dangerous than the sulphuric acid mixture in lead-acid batteries, and crucially, “NiMH batteries have higher power and energy density and a much longer life cycle compared to lead-acid batteries,” according to John M. German in the Encyclopedia of Energy. This energy density is roughly twice that of lead-acid batteries, at roughly 70 Wh/kg.
According to German, NiMH batteries are popular because they are “completely safe and their power output is not affected by the battery state of charge,” meaning voltage output stays consistent until the battery is fully dead. These are all attractive attributes for automotive applications, and indeed, automakers adopted NiMH batteries not long after Ovshinsky’s invention. Many of the late Nineties and early Aughts “first-wave” EVs—developed as a direct response to California government mandates for alternative-fuel vehicles—used NiMH batteries with some success.
General Motors converted from lead-acid to NiMH batteries midway through the production run of the EV1. This effectively doubled the car’s range over the previous lead-acid powerpacks—albeit with significant issues with battery overheating, as NiMH batteries are highly sensitive to heat.
Toyota also used NiMH batteries in the all-electric RAV4 EV, but after a purchase of the patent by Chevron in 2001 and a subsequent lawsuit against Toyota for copyright infringement, the company was forced to discontinue using these batteries as the sole power source for BEVs. (Toyota still uses NiMH batteries for its hybrid battery packs, as the copyright suit did not cover gas-electric hybrid vehicles.)
Still, the infringement lawsuit has led some to believe that the fossil-fuels industry intentionally attempted to suffocate the BEV in its crib. Although automakers insist the interest just wasn’t there for 100-mile EVs that took 18 seconds to reach 60 mph. (The current market for hyper-quick EVs and the appetite for 300 miles of range seems to support this.) What it took for widespread adoption, then, was yet another battery chemistry that could give buyers the range and power they truly wanted.
The Fifth Track on Nirvana’s Nevermind
The advancement that has finally allowed for 300-mile EVs was the mass-production of large lithium-ion (li-ion) batteries. Li-ion batteries have many different specific forms, but they all share one thing in common—a liquid lithium-salt electrolyte. Li-ion batteries have excellent energy density, up to 270 Wh/kg, or quadruple that of an average NiMH battery. In addition, as Jayam Prabhakar Aditya and Mehdi Ferdowsi explain in a 2008 IEEE paper, li-ion batteries boast “light weight… high specific energy, good high-temperature performance, low maintenance,” as well as a low rate of self-discharge relative to NiMH batteries (meaning they don’t lose charge rapidly when unused).
While li-ion batteries in automotive applications aren’t new—the first use was in the 1998 Nissan Altra EV—they are temperamental and development was arduous. A poorly cared for battery is prone to exploding, and li-ion batteries require large amounts of dangerous materials to build, making mass production challenging. Still, their positive attributes and extremely high energy density were appealing, leading both Tesla and Nissan to pursue li-ion battery packs for mass-market vehicles.
The results were indisputable. Tesla, first to market with a production li-ion battery car in the Roadster, used its early R&D to catch “legacy” automakers off guard; Nissan, with the more mundane Leaf, was the first manufacturer to sell over 300,000 BEVs. The long range possible with li-ion batteries meant they were the first technology to convince the public—and automakers—that BEVs were worth pursuing.
Li-ion batteries in automotive use primarily rely on two different chemical compositions, based on the construction of the cathode. The first and most common type is the nickel-manganese-cobalt (NMC) or nickel-cobalt-aluminum (NCA), which is how the most efficient lithium batteries are constructed. Difficulties with sourcing nickel from Russia in the wake of its invasion of Ukraine, however, have led some automakers to pursue a lithium-iron-phosphate (LFP) cathode construction, which is less energy-dense (at 160 Wh/kg vs. NMC’s peak 270 Wh/kg), but easier to source.
After very early dominance by NMC and NCA batteries, LFP batteries now make up roughly 30% of the new EV market, primarily thanks to Chinese automaker BYD and American automaker Tesla’s growing use. Even with the less-energy-dense LFP batteries, Tesla has still managed to squeeze out nearly 300 miles of range in the standard-range Model 3, meaning the difference between NMC and LFP isn’t as significant as that between, say, NiMH and li-ion, or lead-acid and NiMH.
The differences between LFP and NMC batteries may end up being nothing compared to what’s just on the horizon for BEVs, however.
Ceramic Class Gets Electrified
The next advancement on the horizon for batteries is the solid-state lithium battery. A solid-state battery replaces the (highly reactive and flammable) lithium-salt liquid electrolyte of a traditional li-ion battery with a solid electrolyte (usually, a ceramic of some kind). This virtually eliminates the explosive fire risk of li-ion batteries while simultaneously doubling the energy density and increasing overall longevity. According to Allan Paterson, chief technical officer of battery-tech startup Britishvolt, “Solid-state is the holy grail of battery solutions… [they] could dramatically, and positively, change the world of electric vehicles.” Decades of research on finding a suitable solid electrolyte that doesn’t crack under repeated charging, however, have yielded nothing.
That could change in the coming years, however, as Toyota claims its first solid-state lithium battery—with over 600 miles of range—will be hitting the market as early as 2027. Toyota has recently partnered with Japanese oil firm Idemitsu to begin production of the new batteries, with mass production targeted around the end of this decade. Perhaps, at long last, 600-plus-mile mile EVs will finally cure Americans’ range anxiety. Until then, there’s always the Hummer EV’s 2818 pounds of lithium-ion power to help mask your fears.
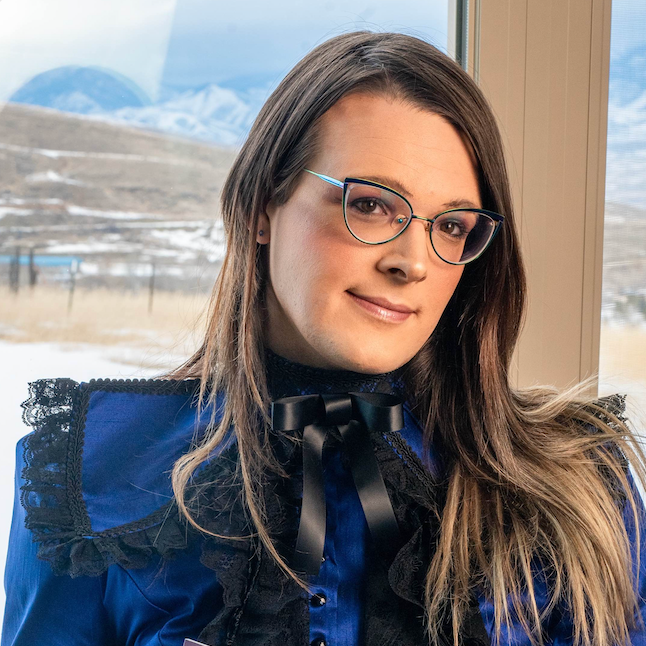
Contributing Editor
Victoria Scott is a freelance writer, photographer, author, and cat mom who lives in Seattle. She is a leading industry expert in catastrophically breaking her vehicles while off-roading. Her proudest moment behind the wheel was completing Mission 34 in Gran Turismo.
Electric vehicles have gone from parlor-trick city runabouts to the main focus of automaker plans at breakneck speed. In 2011, 10,000 battery-electric vehicles (BEVs) were sold in America, an almost meaninglessly infinitesimal fraction of the 11.5 million cars sold that year. Now, analysts predict that 2023 will be the first year where we see one million BEV sales, and half of consumers say they are actively considering an electric vehicle for their next automotive purchase.
One other meaningful trend is noticeable over this same period, and helps explain how EVs have taken the market so rapidly. In 2011, the average BEV sold in America had a paltry 73 miles of range (which just so happens to be the exact EPA range rating of the 2011 Nissan Leaf, the first truly mainstream BEV). That number has quadrupled in the past twelve years, and the average new BEV sold today has 291 miles of range.
This has helped speed adoption, as consumers demand—by huge margins—that their BEVs have over 300 miles of range, according to studies by both Bloomberg and Cox Automotive. Whether people will use that mileage or not is still up for debate, but it’s clear that without the vast leaps in battery technology that have allowed for 300-mile BEVs, the American market share of electric cars would still be measured in tenths of a percent.
So how have automakers fueled this massive leap in range? The short answer is that while batteries are often marketed simplistically, there are large differences as to how they’re built, managed, and integrated into the cars they power. Here’s how EVs have reached such staggering distances—and how 1000-plus mile battery packs may be in the not-too-distant future.
Cells, Interlinked
Batteries are an older concept than the United States. Indeed, Benjamin Franklin was the first person to coin the term “battery”, in 1760, for a device used to store electrical charge. Batteries are all based on the same fundamental concept: Easily preserved chemical potential energy is stored in an inactive state within the battery. By activating a chemical reaction in the battery and releasing the stored potential chemical energy, electricity is produced.
All batteries contain three components to function: two electrical terminals (known as the cathode and the anode) and a chemical substance separating them, known as the electrolyte. Ions flowing through the electrolyte from the anode to the cathode release electricity; ions flowing in the opposite direction recharge the battery. It is a simple concept, but the implementation can be incredibly complex.
The first rechargeable battery was the lead-acid battery, still in use in cars today to run electrical accesories. Most EVs in the early 20th century and stretching all the way into the late Nineties with the GM EV1 used lead-acid batteries as their source of energy. These are a relatively straightforward implementation of the battery concept, with metallic lead and lead dioxide serving as the cathode and anode, and a sulfur solution of some kind as the electrolyte.
While lead-acid batteries are chemically stable, they have a low energy density for their weight—around 35 watt-hours per kilogram—and they tend to degrade rapidly when run to empty repeatedly. Most early lead-acid batteries used diluted liquid sulphuric acid as an electrolyte, which meant if a battery was tipped over, highly dangerous acid would spill out. These early batteries also needed frequent top-ups with water, which turned EV maintenance into an arduous task. As such, early EVs were heavy, high-maintenance machines, with short ranges and massive battery packs, which kept them from widespread viability for decades.
Big Oil vs. Nickel Hydride
The next major development in electric vehicle technology came from the mind of self-taught American inventor Stanford Ovshinsky in the form of the nickel-metal hydride (NiMH) battery. The NiMH battery improves vastly upon the earlier lead-acid form—it uses nickel hydroxide (the “Ni”) as a cathode, an alloy that absorbs hydrogen as an anode (the “MH”), and a potassium hydroxide as an electrolyte. The potassium-hydroxide electrolyte is less dangerous than the sulphuric acid mixture in lead-acid batteries, and crucially, “NiMH batteries have higher power and energy density and a much longer life cycle compared to lead-acid batteries,” according to John M. German in the Encyclopedia of Energy. This energy density is roughly twice that of lead-acid batteries, at roughly 70 Wh/kg.
According to German, NiMH batteries are popular because they are “completely safe and their power output is not affected by the battery state of charge,” meaning voltage output stays consistent until the battery is fully dead. These are all attractive attributes for automotive applications, and indeed, automakers adopted NiMH batteries not long after Ovshinsky’s invention. Many of the late Nineties and early Aughts “first-wave” EVs—developed as a direct response to California government mandates for alternative-fuel vehicles—used NiMH batteries with some success.
General Motors converted from lead-acid to NiMH batteries midway through the production run of the EV1. This effectively doubled the car’s range over the previous lead-acid powerpacks—albeit with significant issues with battery overheating, as NiMH batteries are highly sensitive to heat.
Toyota also used NiMH batteries in the all-electric RAV4 EV, but after a purchase of the patent by Chevron in 2001 and a subsequent lawsuit against Toyota for copyright infringement, the company was forced to discontinue using these batteries as the sole power source for BEVs. (Toyota still uses NiMH batteries for its hybrid battery packs, as the copyright suit did not cover gas-electric hybrid vehicles.)
Still, the infringement lawsuit has led some to believe that the fossil-fuels industry intentionally attempted to suffocate the BEV in its crib. Although automakers insist the interest just wasn’t there for 100-mile EVs that took 18 seconds to reach 60 mph. (The current market for hyper-quick EVs and the appetite for 300 miles of range seems to support this.) What it took for widespread adoption, then, was yet another battery chemistry that could give buyers the range and power they truly wanted.
The Fifth Track on Nirvana’s Nevermind
The advancement that has finally allowed for 300-mile EVs was the mass-production of large lithium-ion (li-ion) batteries. Li-ion batteries have many different specific forms, but they all share one thing in common—a liquid lithium-salt electrolyte. Li-ion batteries have excellent energy density, up to 270 Wh/kg, or quadruple that of an average NiMH battery. In addition, as Jayam Prabhakar Aditya and Mehdi Ferdowsi explain in a 2008 IEEE paper, li-ion batteries boast “light weight… high specific energy, good high-temperature performance, low maintenance,” as well as a low rate of self-discharge relative to NiMH batteries (meaning they don’t lose charge rapidly when unused).
While li-ion batteries in automotive applications aren’t new—the first use was in the 1998 Nissan Altra EV—they are temperamental and development was arduous. A poorly cared for battery is prone to exploding, and li-ion batteries require large amounts of dangerous materials to build, making mass production challenging. Still, their positive attributes and extremely high energy density were appealing, leading both Tesla and Nissan to pursue li-ion battery packs for mass-market vehicles.
The results were indisputable. Tesla, first to market with a production li-ion battery car in the Roadster, used its early R&D to catch “legacy” automakers off guard; Nissan, with the more mundane Leaf, was the first manufacturer to sell over 300,000 BEVs. The long range possible with li-ion batteries meant they were the first technology to convince the public—and automakers—that BEVs were worth pursuing.
Li-ion batteries in automotive use primarily rely on two different chemical compositions, based on the construction of the cathode. The first and most common type is the nickel-manganese-cobalt (NMC) or nickel-cobalt-aluminum (NCA), which is how the most efficient lithium batteries are constructed. Difficulties with sourcing nickel from Russia in the wake of its invasion of Ukraine, however, have led some automakers to pursue a lithium-iron-phosphate (LFP) cathode construction, which is less energy-dense (at 160 Wh/kg vs. NMC’s peak 270 Wh/kg), but easier to source.
After very early dominance by NMC and NCA batteries, LFP batteries now make up roughly 30% of the new EV market, primarily thanks to Chinese automaker BYD and American automaker Tesla’s growing use. Even with the less-energy-dense LFP batteries, Tesla has still managed to squeeze out nearly 300 miles of range in the standard-range Model 3, meaning the difference between NMC and LFP isn’t as significant as that between, say, NiMH and li-ion, or lead-acid and NiMH.
The differences between LFP and NMC batteries may end up being nothing compared to what’s just on the horizon for BEVs, however.
Ceramic Class Gets Electrified
The next advancement on the horizon for batteries is the solid-state lithium battery. A solid-state battery replaces the (highly reactive and flammable) lithium-salt liquid electrolyte of a traditional li-ion battery with a solid electrolyte (usually, a ceramic of some kind). This virtually eliminates the explosive fire risk of li-ion batteries while simultaneously doubling the energy density and increasing overall longevity. According to Allan Paterson, chief technical officer of battery-tech startup Britishvolt, “Solid-state is the holy grail of battery solutions… [they] could dramatically, and positively, change the world of electric vehicles.” Decades of research on finding a suitable solid electrolyte that doesn’t crack under repeated charging, however, have yielded nothing.
That could change in the coming years, however, as Toyota claims its first solid-state lithium battery—with over 600 miles of range—will be hitting the market as early as 2027. Toyota has recently partnered with Japanese oil firm Idemitsu to begin production of the new batteries, with mass production targeted around the end of this decade. Perhaps, at long last, 600-plus-mile mile EVs will finally cure Americans’ range anxiety. Until then, there’s always the Hummer EV’s 2818 pounds of lithium-ion power to help mask your fears.
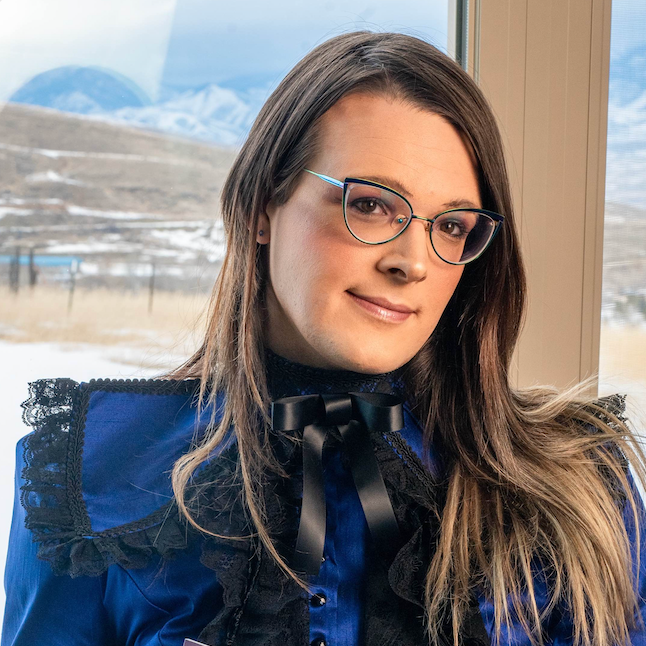
Contributing Editor
Victoria Scott is a freelance writer, photographer, author, and cat mom who lives in Seattle. She is a leading industry expert in catastrophically breaking her vehicles while off-roading. Her proudest moment behind the wheel was completing Mission 34 in Gran Turismo.
Electric vehicles have gone from parlor-trick city runabouts to the main focus of automaker plans at breakneck speed. In 2011, 10,000 battery-electric vehicles (BEVs) were sold in America, an almost meaninglessly infinitesimal fraction of the 11.5 million cars sold that year. Now, analysts predict that 2023 will be the first year where we see one million BEV sales, and half of consumers say they are actively considering an electric vehicle for their next automotive purchase.
One other meaningful trend is noticeable over this same period, and helps explain how EVs have taken the market so rapidly. In 2011, the average BEV sold in America had a paltry 73 miles of range (which just so happens to be the exact EPA range rating of the 2011 Nissan Leaf, the first truly mainstream BEV). That number has quadrupled in the past twelve years, and the average new BEV sold today has 291 miles of range.
This has helped speed adoption, as consumers demand—by huge margins—that their BEVs have over 300 miles of range, according to studies by both Bloomberg and Cox Automotive. Whether people will use that mileage or not is still up for debate, but it’s clear that without the vast leaps in battery technology that have allowed for 300-mile BEVs, the American market share of electric cars would still be measured in tenths of a percent.
So how have automakers fueled this massive leap in range? The short answer is that while batteries are often marketed simplistically, there are large differences as to how they’re built, managed, and integrated into the cars they power. Here’s how EVs have reached such staggering distances—and how 1000-plus mile battery packs may be in the not-too-distant future.
Cells, Interlinked
Batteries are an older concept than the United States. Indeed, Benjamin Franklin was the first person to coin the term “battery”, in 1760, for a device used to store electrical charge. Batteries are all based on the same fundamental concept: Easily preserved chemical potential energy is stored in an inactive state within the battery. By activating a chemical reaction in the battery and releasing the stored potential chemical energy, electricity is produced.
All batteries contain three components to function: two electrical terminals (known as the cathode and the anode) and a chemical substance separating them, known as the electrolyte. Ions flowing through the electrolyte from the anode to the cathode release electricity; ions flowing in the opposite direction recharge the battery. It is a simple concept, but the implementation can be incredibly complex.
The first rechargeable battery was the lead-acid battery, still in use in cars today to run electrical accesories. Most EVs in the early 20th century and stretching all the way into the late Nineties with the GM EV1 used lead-acid batteries as their source of energy. These are a relatively straightforward implementation of the battery concept, with metallic lead and lead dioxide serving as the cathode and anode, and a sulfur solution of some kind as the electrolyte.
While lead-acid batteries are chemically stable, they have a low energy density for their weight—around 35 watt-hours per kilogram—and they tend to degrade rapidly when run to empty repeatedly. Most early lead-acid batteries used diluted liquid sulphuric acid as an electrolyte, which meant if a battery was tipped over, highly dangerous acid would spill out. These early batteries also needed frequent top-ups with water, which turned EV maintenance into an arduous task. As such, early EVs were heavy, high-maintenance machines, with short ranges and massive battery packs, which kept them from widespread viability for decades.
Big Oil vs. Nickel Hydride
The next major development in electric vehicle technology came from the mind of self-taught American inventor Stanford Ovshinsky in the form of the nickel-metal hydride (NiMH) battery. The NiMH battery improves vastly upon the earlier lead-acid form—it uses nickel hydroxide (the “Ni”) as a cathode, an alloy that absorbs hydrogen as an anode (the “MH”), and a potassium hydroxide as an electrolyte. The potassium-hydroxide electrolyte is less dangerous than the sulphuric acid mixture in lead-acid batteries, and crucially, “NiMH batteries have higher power and energy density and a much longer life cycle compared to lead-acid batteries,” according to John M. German in the Encyclopedia of Energy. This energy density is roughly twice that of lead-acid batteries, at roughly 70 Wh/kg.
According to German, NiMH batteries are popular because they are “completely safe and their power output is not affected by the battery state of charge,” meaning voltage output stays consistent until the battery is fully dead. These are all attractive attributes for automotive applications, and indeed, automakers adopted NiMH batteries not long after Ovshinsky’s invention. Many of the late Nineties and early Aughts “first-wave” EVs—developed as a direct response to California government mandates for alternative-fuel vehicles—used NiMH batteries with some success.
General Motors converted from lead-acid to NiMH batteries midway through the production run of the EV1. This effectively doubled the car’s range over the previous lead-acid powerpacks—albeit with significant issues with battery overheating, as NiMH batteries are highly sensitive to heat.
Toyota also used NiMH batteries in the all-electric RAV4 EV, but after a purchase of the patent by Chevron in 2001 and a subsequent lawsuit against Toyota for copyright infringement, the company was forced to discontinue using these batteries as the sole power source for BEVs. (Toyota still uses NiMH batteries for its hybrid battery packs, as the copyright suit did not cover gas-electric hybrid vehicles.)
Still, the infringement lawsuit has led some to believe that the fossil-fuels industry intentionally attempted to suffocate the BEV in its crib. Although automakers insist the interest just wasn’t there for 100-mile EVs that took 18 seconds to reach 60 mph. (The current market for hyper-quick EVs and the appetite for 300 miles of range seems to support this.) What it took for widespread adoption, then, was yet another battery chemistry that could give buyers the range and power they truly wanted.
The Fifth Track on Nirvana’s Nevermind
The advancement that has finally allowed for 300-mile EVs was the mass-production of large lithium-ion (li-ion) batteries. Li-ion batteries have many different specific forms, but they all share one thing in common—a liquid lithium-salt electrolyte. Li-ion batteries have excellent energy density, up to 270 Wh/kg, or quadruple that of an average NiMH battery. In addition, as Jayam Prabhakar Aditya and Mehdi Ferdowsi explain in a 2008 IEEE paper, li-ion batteries boast “light weight… high specific energy, good high-temperature performance, low maintenance,” as well as a low rate of self-discharge relative to NiMH batteries (meaning they don’t lose charge rapidly when unused).
While li-ion batteries in automotive applications aren’t new—the first use was in the 1998 Nissan Altra EV—they are temperamental and development was arduous. A poorly cared for battery is prone to exploding, and li-ion batteries require large amounts of dangerous materials to build, making mass production challenging. Still, their positive attributes and extremely high energy density were appealing, leading both Tesla and Nissan to pursue li-ion battery packs for mass-market vehicles.
The results were indisputable. Tesla, first to market with a production li-ion battery car in the Roadster, used its early R&D to catch “legacy” automakers off guard; Nissan, with the more mundane Leaf, was the first manufacturer to sell over 300,000 BEVs. The long range possible with li-ion batteries meant they were the first technology to convince the public—and automakers—that BEVs were worth pursuing.
Li-ion batteries in automotive use primarily rely on two different chemical compositions, based on the construction of the cathode. The first and most common type is the nickel-manganese-cobalt (NMC) or nickel-cobalt-aluminum (NCA), which is how the most efficient lithium batteries are constructed. Difficulties with sourcing nickel from Russia in the wake of its invasion of Ukraine, however, have led some automakers to pursue a lithium-iron-phosphate (LFP) cathode construction, which is less energy-dense (at 160 Wh/kg vs. NMC’s peak 270 Wh/kg), but easier to source.
After very early dominance by NMC and NCA batteries, LFP batteries now make up roughly 30% of the new EV market, primarily thanks to Chinese automaker BYD and American automaker Tesla’s growing use. Even with the less-energy-dense LFP batteries, Tesla has still managed to squeeze out nearly 300 miles of range in the standard-range Model 3, meaning the difference between NMC and LFP isn’t as significant as that between, say, NiMH and li-ion, or lead-acid and NiMH.
The differences between LFP and NMC batteries may end up being nothing compared to what’s just on the horizon for BEVs, however.
Ceramic Class Gets Electrified
The next advancement on the horizon for batteries is the solid-state lithium battery. A solid-state battery replaces the (highly reactive and flammable) lithium-salt liquid electrolyte of a traditional li-ion battery with a solid electrolyte (usually, a ceramic of some kind). This virtually eliminates the explosive fire risk of li-ion batteries while simultaneously doubling the energy density and increasing overall longevity. According to Allan Paterson, chief technical officer of battery-tech startup Britishvolt, “Solid-state is the holy grail of battery solutions… [they] could dramatically, and positively, change the world of electric vehicles.” Decades of research on finding a suitable solid electrolyte that doesn’t crack under repeated charging, however, have yielded nothing.
That could change in the coming years, however, as Toyota claims its first solid-state lithium battery—with over 600 miles of range—will be hitting the market as early as 2027. Toyota has recently partnered with Japanese oil firm Idemitsu to begin production of the new batteries, with mass production targeted around the end of this decade. Perhaps, at long last, 600-plus-mile mile EVs will finally cure Americans’ range anxiety. Until then, there’s always the Hummer EV’s 2818 pounds of lithium-ion power to help mask your fears.
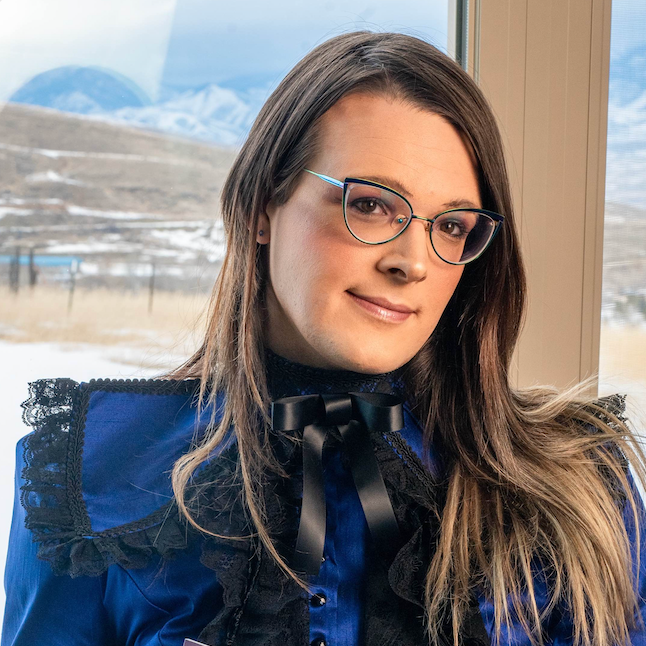
Contributing Editor
Victoria Scott is a freelance writer, photographer, author, and cat mom who lives in Seattle. She is a leading industry expert in catastrophically breaking her vehicles while off-roading. Her proudest moment behind the wheel was completing Mission 34 in Gran Turismo.